|
|
04/10/2024 |
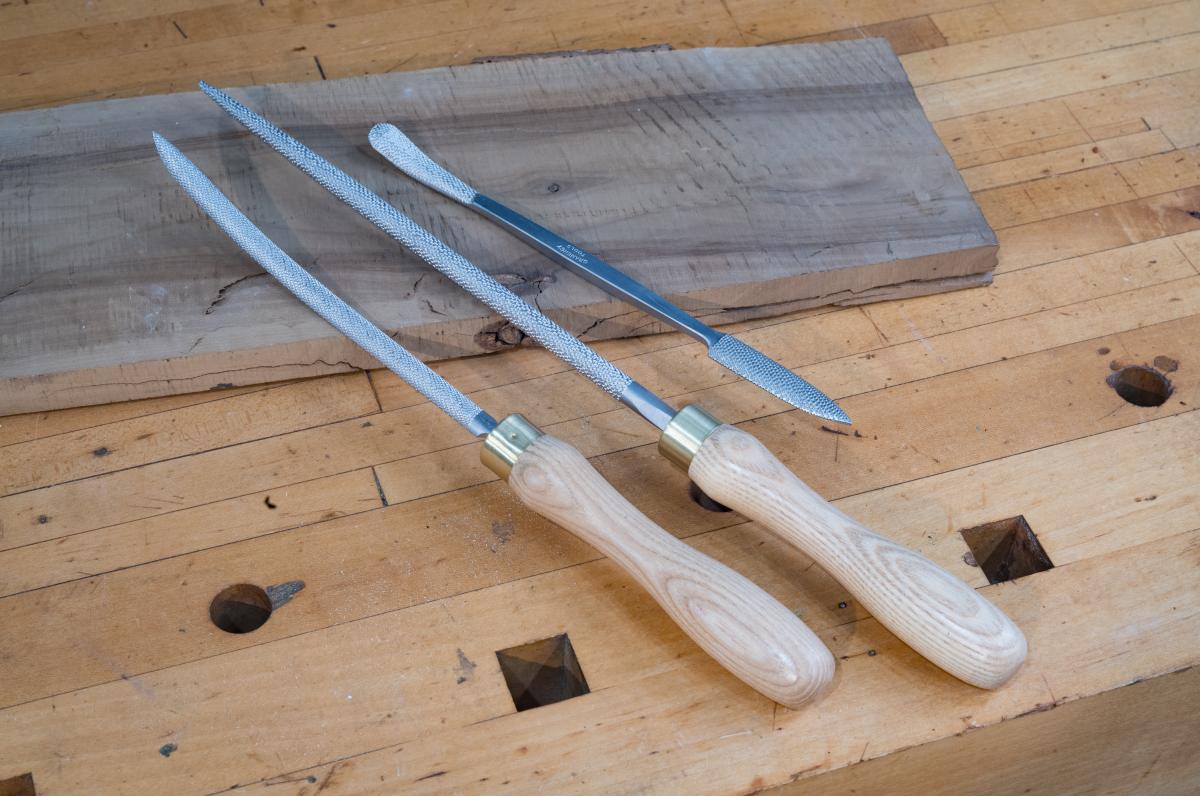
As many of you already know from experience, hand-cut rasps cut smoother and faster than machine-made rasps. For nearly 20 years, we have been selling hand-cut rasps to a great reception. The range we have offered, however, has been pretty static for a bunch of years. The Gramercy Cabinet Rasps and Modeller's Rasps cover most cabinetmakers' needs. We have also added a couple of sets of riffler files for smaller, more detailed work. The only real innovation has been the Saw Handle Maker's Rasp, which is both bent and then toothed on one side, so that you can shape the inside of a handle without accidentally damaging the material opposite.
Over the years we have gotten suggestions and requests for other styles. In the last few months I've been thinking about new permutations of rasps that might be useful to woodworkers and wood carvers. For example, riffler rasps are doubled ended with complementary shapes on each end. The theory is that you can do one operation with one end and then do a complementary operation with the head that is on the other end - you just flip the rasp over in your hand. The actual complementary pairs of shapes are traditional and date from when the biggest use of rasps was in shaping wooden patterns for the foundry industry. The hand shaped wooden pattern is mostly a thing of the past, but the shapes and pairings of the rifflers remain. So we wondered: what would happen if we took two very useful ends of a rifler that are typically on different rifflers and put them together on one rasp? So that's where the new Fine Riffler design comes from.
The second new rasp is simply a longer, thicker Gramercy Tools Rat Tail rasp. I find rat tails espeically handy for decorative work, and a longer, thicker one simply made sense. So there's the second design.
The third new rasp is a customer suggestion - actually the suggestion of several customers. The original Saw Handle Maker's rasp wasn't my own idea; it came about from a suggestion by Larry Williams, the acclaimed planemaker. Its design makes it really easy to shape the inside of a handle or anything that has an opposing surface close by, because the curve is bent up so you don't hit the other side (and even if you do, only one side of the rasp has teeth). We had requests for a narrower version of the same thing. With an narrower rasp, you got a tighter radius on the half roundness of the file. This translates into a freedom to do tighter curves. And in certain situations, the narrower rasps fits the space better.
We are very pleased to announce these new rasps and we have more still to come. They may help solve a specific problem that some of you are working on today, and going forward we hope they open up new possibilities and capacities for fabrication. And that is very exciting indeed.
|
Join the conversation |
|